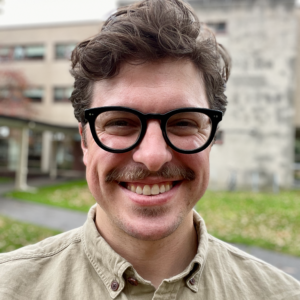
Nicholas Anway is a student at Harvard Law School.
Candace Dixon could barely climb the stairs. After lifting nearly 100,000 items in two months of working with robots at an Amazon fulfillment center, her back was severely damaged by bulging discs, inflammation, and chronic pain. Her doctor attributed her injuries “100 percent” to her workplace — and did not expect them to improve.
As a “stower,” Dixon’s job was to stand at a station, one of hundreds on the warehouse floor, and fill 8-foot-tall merchandise racks with consumer products using a stepladder. The racks were mounted atop wheeled, orange robots, which would transport them from station to station. Another worker, called a “water spider,” supplied her station with an endless stream of boxes full of products. Dixon would unbox the products and place them into the racks, squatting to lift the heavy ones and climbing her stepladder to stow others. Then, she’d scan their new locations on the rack. To hit her quota, Dixon had to scan and place a new item every 11 seconds. “‘The clock was always ticking,’” she told Reveal. “As soon as she’d filled a rack, she’d press a button and one robot would zip it away while another robot would bring a new one to fill.”
Robots aren’t new to workplaces. In the United States, robotics have been used in manufacturing for over half a century. But today, industrial robots are being integrated into workplaces at unprecedented scale, driven by advances in machine learning and robotics technology, and by a corporate tack towards automation in the wake of the Great Recession. A 2019 report from the Century Foundation estimated the number of manufacturing robots to be one per five-hundred workers, a rate which has more than doubled since 2009.
The twenty-first century surge in industrial robot integration extends well beyond manufacturing. Amazon — the second-largest private employer in the U.S., behind only Walmart — is leading a parallel robotics race in the warehousing industry, which is changing the workplaces of over one million workers in the U.S. As of 2021, Amazon reported that about 350,000 mobile drive unit robots, “drives” for short, were working alongside employees at fulfillment centers worldwide. More than 200,000 drives are operating in the company’s robotics fulfillment centers in the U.S.
Proponents at Amazon argue that robotics integration has the potential to improve working conditions for warehouse employees. In facilities without robots, for example, Amazon warehouse workers often walk 10 to 20 miles per day on hard concrete floors transporting items. Facilities with robots have largely eliminated this task.
Yet recent reporting casts doubt on this sanguine view of Amazon’s approach to human-robot interaction. Workers like Dixon are being injured in Amazon’s robotics-integrated facilities at alarming rates. With her workers’ compensation settlement running thin, Dixon told Reveal that “[s]he was struggling to land a new job and worried she’d lose her home.” Due to her injuries, she was left largely unable to work.
Ms. Dixon isn’t alone. Since 2019, at least three investigative reports — from Reveal, the Strategic Organizing Center, and the Washington Post — have concluded that Amazon warehouses are unusually unsafe. In the U.S., the Post reported that there were 5.9 serious workplace injuries per 100 employees at Amazon warehouses in 2020 — nearly double the rate of non-Amazon warehouses. Walmart, by comparison, reported 2.5 serious injuries per 100 workers at its warehouses that year.
Amazon’s robotics fulfillment centers are more dangerous still. According to the SOC report, Amazon’s “facilities with robotic technology had a serious injury rate of 7.9 per 100 workers [in 2019], more than 54 percent higher than the serious injury rate at non-robotic . . . facilities in the same year.” That finding is corroborated by Reveal’s report, which also found “a correlation between robots and safety problems, such as in Tracy, California, where the serious injury rate nearly quadrupled in the four years after robots were introduced.” In 2018, Dixon’s injury was one of 422 recorded at the robotics-driven warehouse in which she worked.
The three reports suggest that the higher workplace injury rates in robotics fulfilment centers are caused both by management’s inhumane approach to robotics integration and by the increasingly repetitive and demanding nature of robotics-integrated warehouse work. Amazon warehouse employees work 10- to 12-hour shifts with one 30-minute and two 15-minute breaks. During their shifts, they are closely monitored to ensure that they keep pace with robots. According to the SOC report, “[w]hen a worker picks or stows an item, a timer starts counting down, tracking the seconds until the worker picks or stows the next item.” Every gap in scanning is labeled a “time off task,” which can lead to punitive action from management. Even bathroom breaks are surveilled. One worker developed urinary tract infections while working in the same warehouse as Dixon. “You have to hold your pee or not make your rate,” another told Reveal. These are examples of management choices, not technology putting workers at risk of injury.
Workers are also forced to perform repetitive movements quickly for long periods of time, which can lead to injury if not executed perfectly. According to the New York Times, this element of robotics integration has increased the average worker’s productivity targets from around 100 items per hour to 300–400 by isolating the tasks that workers are asked to perform — scanning rather than walking, for example. Dixon’s scan rate — more than 300 items per hour — was closely monitored by management through automated surveillance. Like many other Amazon warehouse workers, if she didn’t hit her target speed she would be written up and, absent improvement, fired.
This approach to optimizing worker productivity for robotics-integration may explain the relationship between Amazon’s one-two punch in 2018, the year of Dixon’s injuries: more holiday items shipped than the year before with 20 percent fewer seasonal workers, and a higher serious injury rate than any other firm studied in the three reports among the workers that it did employ.
In his final annual letter to shareholders, former Amazon CEO, Jeff Bezos, acknowledged that the company needs to “do a better job” for its employees, pledging “to be Earth’s Best Employer and Earth’s Safest Place to Work.” Shortly thereafter, Amazon announced a $12 million contribution and five-year partnership with National Safety Council aimed at reducing musculoskeletal disorders like those suffered by Ms. Dixon.
But these symbolic gestures fall short of addressing the fundamental problem with Amazon’s robotics program: efficiency-driven profit margins don’t justify the toll that it is taking on warehouse workers’ bodies — and they never will.
To avoid workplace injuries, warehouse workers should be involved in the design of robot-integration from the beginning. MIT Industrial Relations Professor Thomas Kochan has written extensively about the important role that workers can play in building integrated technological systems that increase efficiency and prioritize worker wellbeing. “To get the best returns from technology,” Kochan writes, “technology and work design should be integrated, not developed in a sequential process where technology design is determined prior to and apart from considering its effects on work and the workforce.” The failure to adopt such a strategy may explain why for so many warehouse workers, Amazon’s approach to robotics integration has come with workplace safety sticker shock.
Daily News & Commentary
Start your day with our roundup of the latest labor developments. See all
July 1
In today’s news and commentary, the Department of Labor proposes to roll back minimum wage and overtime protections for home care workers, a federal judge dismissed a lawsuit by public defenders over a union’s Gaza statements, and Philadelphia’s largest municipal union is on strike for first time in nearly 40 years. On Monday, the U.S. […]
June 30
Antidiscrimination scholars question McDonnell Douglas, George Washington University Hospital bargained in bad faith, and NY regulators defend LPA dispensary law.
June 29
In today’s news and commentary, Trump v. CASA restricts nationwide injunctions, a preliminary injunction continues to stop DOL from shutting down Job Corps, and the minimum wage is set to rise in multiple cities and states. On Friday, the Supreme Court held in Trump v. CASA that universal injunctions “likely exceed the equitable authority that […]
June 27
Labor's role in Zohran Mamdani's victory; DHS funding amendment aims to expand guest worker programs; COSELL submission deadline rapidly approaching
June 26
A district judge issues a preliminary injunction blocking agencies from implementing Trump’s executive order eliminating collective bargaining for federal workers; workers organize for the reinstatement of two doctors who were put on administrative leave after union activity; and Lamont vetoes unemployment benefits for striking workers.
June 25
Some circuits show less deference to NLRB; 3d Cir. affirms return to broader concerted activity definition; changes to federal workforce excluded from One Big Beautiful Bill.